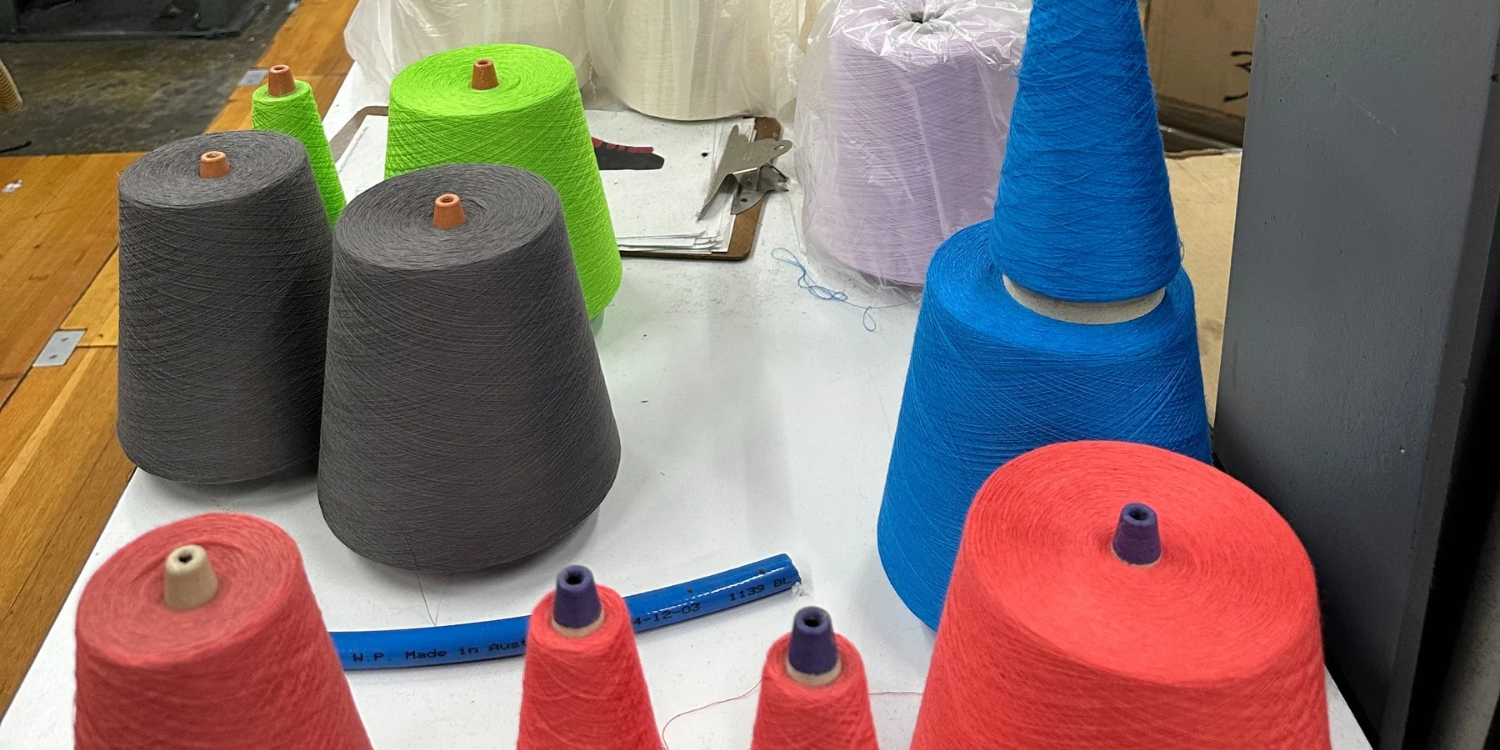
Wilderness Wear: The heartbeat of Australian Merino manufacturing
My affinity and trust in Wilderness Wear began back when I deployed to Afghanistan in 2007. Arriving in the hot summer of August where daytime temperatures would hit the high 40s with cold nights and staying on over the winter period where we would experience night times of -20c the extreme weather demanded a technical layering system. We would be operating deep in the mountains and often for weeks at a time living out of open topped cars and walking for miles each night to conduct missions.
In a swag of cold weather kit happened to be an ensemble of 100% merino base layers from Wilderness Wear with an Australian owned and made logo on them. 100% Merino was chosen due to its resistance to fire (a big lesson learned from the early Under Armour days of the Iraq War) and its ability to resist odour and feel fresh after weeks of unwashed use.
Fast forward 17 years and I still pull those Wilderness Wear tops out of my old Army kit and use them. Some are worn out in places; others look brand new, with my record for wearing them well over three weeks without washing them nor myself. The trust that Wilderness Wear earned by Special Forces operating in winter in Afghanistan is why it has earned a place on the shelves of PAST Outdoors.
On a recent trip to Melbourne, Jon, the Chief Operations manager, invited me to tour the design lab, manufacturing plant, and outlet store of Wilderness Wear in the Melbourne suburb of Preston. Having a trade background, I get a little excited going behind the scenes to see how things are made, and that day was no exception.
Jon greeted me at the door to the show room and took me straight through a set of doors to the warehouse stacked high with boxes of merino yarn, finished products and staff meticulously packing orders for independent stores around the country and even Japan.
As we walked closer to the manufacturing plant the gentle hum and pulse-like sound of the sock weaving machines filled the air and as you entered and saw a web of yarn, wires, rails and the subtle smell of lanolin filled the air. As we enter, smiling faces stick their heads up from behind various work stations and give me a nod or a wave.
Jon proudly shows me the machines stacked with rolls of coloured merino yarn, hi-tech polypropylene and nylons for providing strength and articulation to the socks and garments and then points me to a relic of a computer that reminds me of my childhood (and early days in Defence) where a pile of floppy discs sits next to the yellowed-white ancient box. The place where merino wool sock designs are laid out flat on a bitmap to plot into the retro looking Italian made sock weavers.
I watch as socks are being knitted into long tubes, turned inside out by hand and passed to the next stage of the ends being sewn into a sock. The socks take about 20 minutes to knit and close the ends before being washed, pressed, folded then sent to quality control. In the QC room they are inspected by hand and presented in cardboard packaging with three pairs placed into a compostable bag ready for shipping. Not seeing those horrible plastic hangers, tags and bags was a welcome sight for me and our oceans.
As we take some time sitting upstairs on the cutting table looking down at the factory floor Jon and I chat about how amazing it is that manufacturing like this is still alive in our suburbs. He tells me stories about the staff who are from all walks of life – the lead sock maker (yes that’s his trade and there are not many like him) is 84 years young and is back after several retirements enjoying the day like it is his first! I hear stories of refugees from the Vietnam War, skilled migrants who have bought critical trades that we have lost as we pushed manufacturing off-shore and workers recruited from the disability sector who have found purpose, family and friendships within this tiny little bespoke Merino manufacturing plant.
We decide to get lunch before we get down to ordering the next year's range and I thank Jon and tell him how grateful I am for the tour and how fascinating it was. We don’t even notice the noise anymore as we chat (I’m pretty deaf from my Army and trade days) and Jon makes a comment that is stuck in my mind “The noise, I don’t find it offensive, it’s kind of like the sound of the heartbeat of Wilderness Wear”.
I returned to our store the following day, excitedly telling all the staff the process I just witnessed and we all looked at our bright coloured rack of Wilderness Wear socks and took time to revisit our range. I can’t look at them the same anymore. Each pair of socks has been handled by up to twelves sets of hands to get where they are, real hands, real people with a story and right here in Australia.
1 comment
Great write-up – certainly endorses my decision to look to Wilderness Wear before anywhere else.
Kevin Cameron
Leave a comment
This site is protected by hCaptcha and the hCaptcha Privacy Policy and Terms of Service apply.